Product Overview
Screening Systems: Center Flow Screen | Dual Flow Screen | Filter Screen | Multi Rake Bar Screen | Basket Screen | Grab Bar Screen | Trash Rack Screen | Fine Screen Horizontal | Screw Screen | Rotary Drum Screen | Compact Screening | Storm-water Screen | Vertical Screw Screen | Sludge Screen
Screenings & Sludge Handling: Compacting Conveyor | Back Pressure Device | Screening Washing Press | Screenings Cutter
Transport Systems: Container Handling System | Skip Hoist System | Screw | Launder Trough
Septage Receiving: Compact-Screening | Septage Receiving Station Grit Treatment: Grit Receiving Station | Grit Classifier | Grit Wash Unit | Drum Screen
Compact Units: Compact Plant KSF-K | Compact Plant KSF-L
Filter Screen
Functional Principle
The waste water flows through perforated filter elements made of Stainless Steel, while contaminants are held back. Solid matter is picked up directly at the bottom of the channel without necessarily requiring a base step. The filter elements form a continuous filter belt which is cleaned by a brush at the upper deflection point. The cleaning process is assisted by a series of jets working in proportion to the screenings load. Tines located on every 5th screening element prevent build-up of rolling matter in front of the screen and ensure that large matter is removed. The sheet steel side plates of the filter elements slide on plastic rails on the screen frame, thus forming a seal and preventing screenings from being washed past the screen at the sides. As a result of the half-round shape of the filter elements and the arrangement of the cleaning brush at the upper deflection point, the distance between the brush and the filter element remains constant. This constant distance ensures very effective cleaning combined with low wear of the brush. At the turning points of the chain drive, the filter elements are in contact with one another via their sealing areas. The gap between the elements thus remains constant and small at all times during the rotation cycle, including at the upper and lower deflection points. Official, independent tests have shown that our screens with a hole size of 6 mm approx. filter out double the amount of screenings as a stage screens with 6 mm gap size. The screenings retention figure of our screen with 6 mm holes is of the order of 85%. The efficiency of our filter screens prevents build-up of screeningsand clogging up in the WWTP and thus avoids time-consuming and costly measures to deal with these disturbances.
Features
- Reliable / Robust Construction
- No malfunctioning
- Handle large amount oil/grease
- Segment of circle allows optimal cleaning
Dimensions | |
---|---|
Filter Width | 300 to 3,000 mm |
Shaft Center Distance | Up to 11,000 mm, larger sizes on request |
Filter Element Hole Size | 2 to 12 mm, other sizes on request |
Water Level Difference | Up to 2 m, larger differentials on request |
Mounting Angle | 75°, 60° or 50°, other angles on request |
Note: SS304, SS316 & other materials on request. |
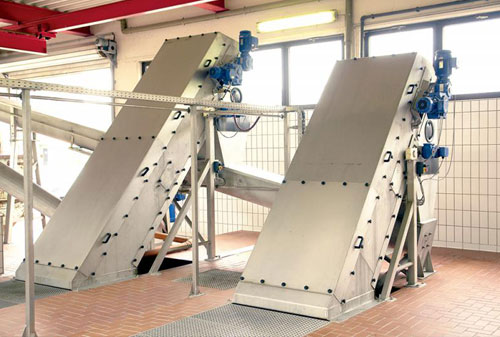
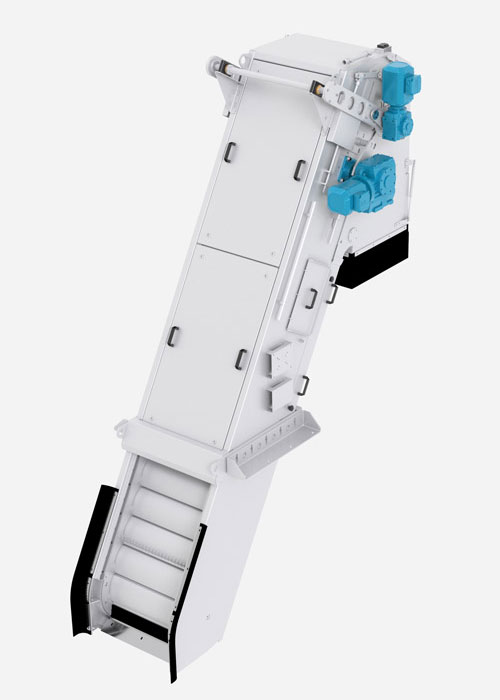
Multi Rake Bar Screen
Functional Principle
The waste water flows through bars made of stainless steel, while contaminants are held back. Solid matter is picked up directly at the bottom of the channel without the need for a bottom recess. The cleaning elements are fixed between two chains and are designed with teeth for the best cleaning of the screen. The screenings can be discharged into containers, wash compactors, screw conveyors, conveyor belts etc.
Features
- Reliable / Robust Construction
- No malfunctioning
- Coarse matter discharge through large rakes
- Suitable for changes in operating conditions
- Hygienically Encapsulated
Dimensions | |
---|---|
Filter Width | 300 to 6,000 mm |
Shaft Center Distance | Up to 25,000, larger sizes on request |
Slot Opening | 2 to 100 mm, other sizes on request |
Water Level Difference | Up to 2 mm, larger differentials on request |
Mounting Angle | 95°, 75° or 60°, other angles on request |
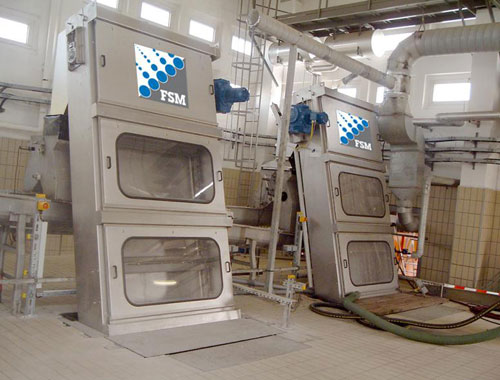
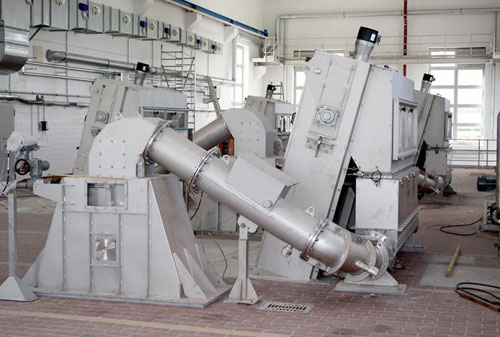
Screw Screen
Functional Principle
The waste water flows through a perforated basket. The installation angle is 35° or 90°. The basket is fixed and cleaned by a rotated screw with a cleaning brush. The screening is transported, washed and compacted by one screw. This design guaranteed that no screening can pass the screen by “carryover” effect.The screw is designed in the dewatering zone with shaft to reduce the wear and prevent a blockage. Perforation for the screen basket is from 2 mm up to 10 mm. The cleaning of the basket is performed by a brush. The drive is realized by a gear motor at the top.
Features
- Reliable / Robust Construction
- No additional cleaning required
- Hygienically Encapsulated
- Suitable for Outdoor application
Dimensions | |
---|---|
Screen Width | 200 to 600 mm |
Perforation | 2 to 10 mm, other sizes on request |
Installation Angle | 35° and 90°, other angles on request |
Note: SS304, SS316 & other materials on request. |
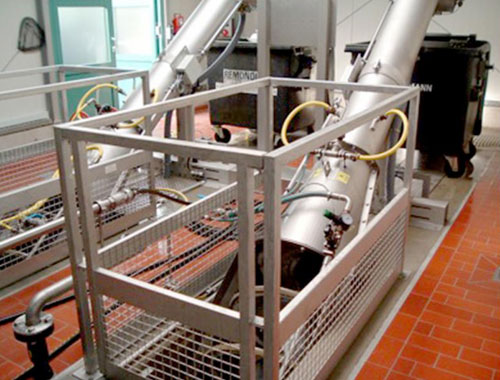
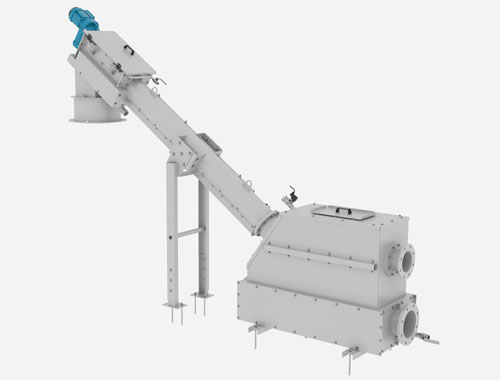
Rotary Drum Screen
Functional Principle
Waste water flows through a revolving drum, which is installed at an angle of 35°. The wastewater flows into the open end of the drum. Floating and suspended screenings are retained by the screen basket, which is available with a perforation or a wedge wire. The upper third of the drum is cleaned via a line of nozzles.The screenings thereby separated out drop into the screw conveyor, which transports and compacts the screenings. The design ensures that the screen side to be cleaned is always in the upstream water, avoiding the “carry-over” effect. Perforation size/Bar spacing of the screening area can be between 1 / 0,5 mm and 10 / 6 mm. Cleaning of the drum is effected by a spray nozzle bar and a brush. Drum and conveyor are driven by a geared motor. Our rotary drum screen could be installed directly into a channel or as an option into a tank.
Features
- Reliable / Robust Construction
- Low head loss
- Cleaning up to 120 Bar available
- No malfunctioning Dimensions
Dimensions | |
---|---|
Diameter | 500 to 3,000 mm |
Perforation | 1 to 10 mm, other sizes on request |
Bar Spacing | 0,5 – 6 m, other sizes on request |
Installation Angle | 35°, other angles on request |
Note: SS304, SS316 & other materials on request. |
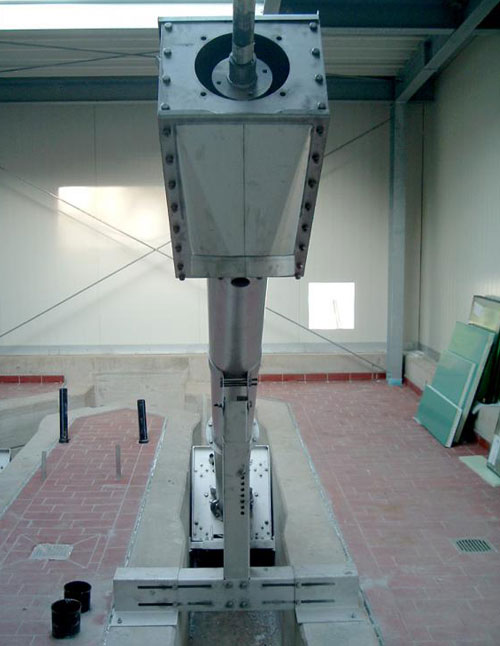
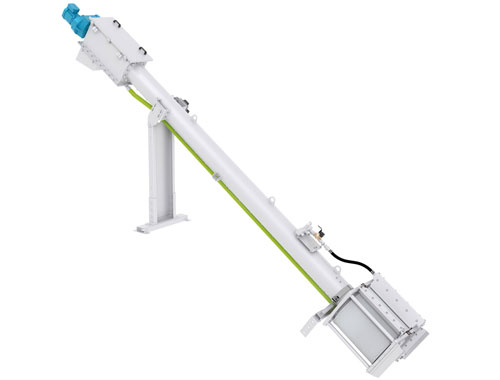
Compacting Conveyor
Functional Principle
Our compacting conveyor is available in 3 sizes with screw diameters of 200, 300 and 400 mm. It is used to dewater, compact and convey screenings or other damp/wet waste materials. Waste materials from a screen, screw conveyor or conveyor belt are dropped into the inlet hopper.The worm screw conveys, dewaters and compacts the waste material. The water escaping from the compacted material is released to the flume.An optional available washing device, washes out more than 90% of faecal matter. Hair, fibres etc. which could cause operating failures and build-ups remains in the screenings. Service water can be used as wash water. The unit is driven by an SEW geared motor.If the installation is used outdoors, the machine can be provided with heating.
Features
- Reliable / Robust Construction
- 95% made of Stainless Steel
- Gas-tight compacting system
- Easy retrofit / replacement
- Hygienically Encapsulated
Dimensions | |
---|---|
Type | SFC 200, 300, 400 |
Diameter of screw | 200, 270, 370 mm |
Throughput | 2, 4 up to 10 m3/hr pipe screening |
Solid Matter | > 30 % |
Faecal Matter | > 90% |
Volume/Weight Reduction | 40 – 60% |
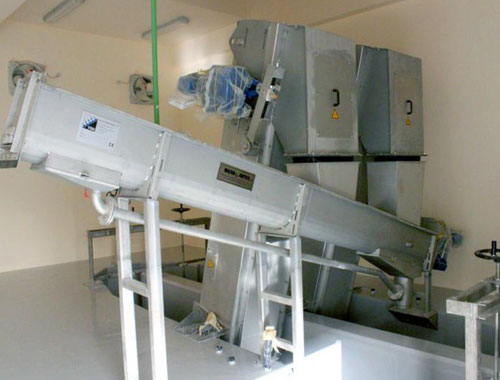
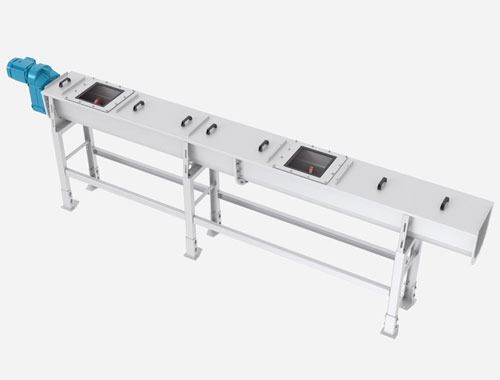
Grit Wash Unit
Functional Principle
The grit/water mixture is fed in via the inlet flange of the grit wash tank. Organic matter is held in suspension and floated off while the grit is sedimented in the tank. With the addition of water, the sedimented grit is separated from the remaining organic constituents using a stirring device and up-current technique. The grit is removed from the tank, de-watered and discharged via a discharge screw.With the addition of a bunker at the upstream side, our grit wash unit can be extended to become a reception station for sewer grit. If a fractionating and washing drum is positioned between the bunker and the wash unit, the installation can be additionally used for conditioning street sweepings.
Features
- Reliable / Robust Construction
- Suitable for upstream application
- Volatile solids can be reduced < 3 %
- Can be fine-tuned up to 30 l/s
Dimensions | |
---|---|
Size | 5200 x 2200 x 3120 mm, others on request |
Throughput | Up to 40 l/s, others on request |
Installation Size | SWA 10, 18, 30, 40 & TB-SWA |
Separating Capacity | > 95 % of particle size 0.2 mm |
Note: SS304, SS316 & other materials on request. |
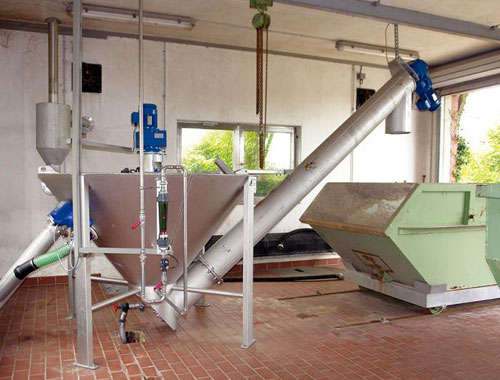
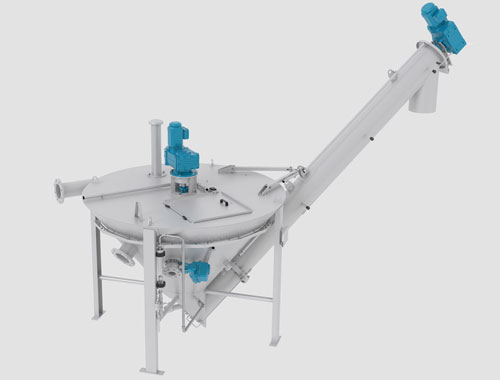
Drum Screen
Functional Principle
The drum screen can be charged via feed pipe, free flow supply or screw conveyor. Material which does not pass through the perforations remains in the screening drum in accordance with hole size. A line of nozzles assists separation of small matter from large matter and washes off e.g. adhering grit. Washed off matter flows through the perforations with the wash water and passes to a collection tank from which it can be fed to a further treatment stage.If desired by customer, the screening drum can be provided with a series of perforations of differing sizes. This enables various fractions with different grain sizes to be obtained.
Features
- Reliable / Robust Construction
- Suitable for pre-separation of organic matter
- Easy retrofit / replacement
- Suitable for outdoor application
- Hygienically Encapsulated
Dimensions | |
---|---|
Size | On request |
Diameter | 500 to 2,000 mm, others on request |
Throughput | On request |
Perforation | 2 – 40 mm, other sizes on request |
MOC | SS304 | SS316 | others on request |
Drives | Gear operated |

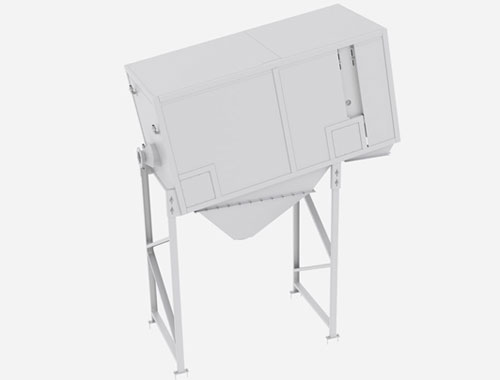